In the ever-evolving landscape of modern commerce, efficient warehouse management is pivotal to success. A crucial decision that warehouse managers face is whether to rely on manual handling or embrace warehouse automation. Each approach comes with its unique advantages and drawbacks, and choosing the right one can significantly impact a company’s operations, costs, and competitiveness.
This blog post explores the factors that influence the choice between manual handling and warehouse automation, shedding light on when and why manual handling may be a better option for certain businesses.
By understanding the scenarios where manual labor excels, you can make an informed decision that aligns with your specific operational requirements, budget constraints, and long-term goals.
Before we go further into this topic, don’t forget to follow my LinkedIn account. You’ll get more helpful insights on supply chain management there.
Table of Contents
Low Volume or Seasonal Operations
One key scenario where manual handling often trumps warehouse automation is in businesses dealing with low inventory volumes or experiencing seasonal fluctuations.
Investing in expensive automation equipment may not be cost-effective when demand for your products varies significantly throughout the year.
Manual labor offers flexibility that automated systems struggle to match. When you rely on human workers, you can easily adjust your workforce to meet changing demand levels.
During peak seasons, you can hire temporary workers, and during slower periods, you can reduce your labor force accordingly. This adaptability can save you substantial capital expenses on automation machinery that would otherwise remain underutilized for a significant portion of the year.
Moreover, manual handling allows you to respond quickly to unforeseen changes in demand. If you suddenly experience a surge in orders due to unexpected events or promotions, you can scale up your workforce on short notice, avoiding costly delays associated with acquiring and configuring automation equipment.
Customization and Variety
Warehouses that handle a diverse range of products, each with unique characteristics, can find manual handling more suitable than warehouse automation.
Products come in various shapes, sizes, and packaging, and configuring automated systems to handle these variations can be time-consuming and expensive.
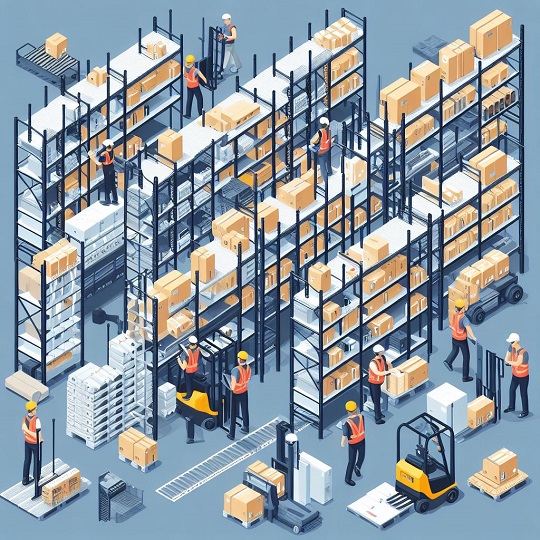
Manual labor excels in adapting to these variations. Human workers can quickly adjust their methods and techniques to suit the specific requirements of each product.
Whether it’s fragile items that require extra care or irregularly shaped objects that don’t fit neatly onto conveyor belts, human dexterity and problem-solving abilities are valuable assets.
Furthermore, the cost of reconfiguring automated systems for each new product type or packaging change can be prohibitive, especially for businesses with frequently changing product lines. Manual handling allows you to avoid these reconfiguration costs and maintain operational flexibility.
Initial Capital Constraints
Another important consideration when choosing between manual handling and warehouse automation is your budget. Automated systems can be prohibitively expensive to purchase and install, making them a less viable option for businesses with limited capital resources.
For many small and medium-sized enterprises (SMEs) or startups, it may be more practical to start with manual processes and gradually invest in automation as the business grows and finances become available.
This staged approach allows you to allocate your budget strategically and assess the impact of automation on your operations before committing to a full-scale implementation.
Additionally, by initially focusing on manual handling, you can allocate your budget to other critical aspects of your business, such as marketing, product development, or expanding your customer base. As your revenue grows, you can reinvest in automation where it makes the most sense.
You might also like:
- How to Implement the FIFO Method in Your Inventory Management: A Step-by-Step Guide for You
- Why Wasting Employee Skills Is a Costly Missed Opportunity
Rapid Changes in Product or Process
In industries characterized by rapid changes in products, processes, or market demands, manual handling can provide a distinct advantage. Automated systems are designed for efficiency and consistency, but they may struggle to keep up with frequent changes.
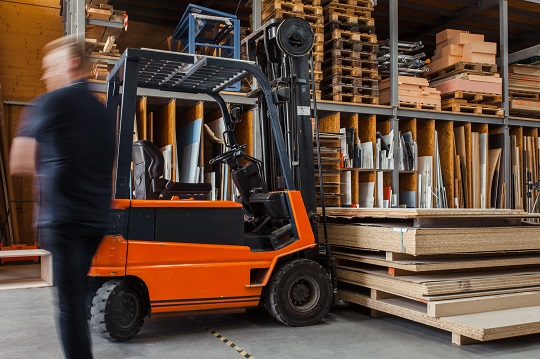
If your warehouse frequently introduces new product lines or adjusts operational processes, the time and cost required to reprogram or reconfigure automated systems can outweigh the benefits they provide.
In such dynamic environments, manual labor offers a level of adaptability and responsiveness that automation struggles to match.
For instance, suppose you’re in the fashion industry, where trends change rapidly, or in the electronics sector, where product specifications evolve continuously.
In that case, manual handling allows you to quickly shift your workforce to accommodate these changes without experiencing significant downtime or costly system modifications.
Maintenance and Repairs
Automation systems, while efficient, require regular maintenance and can experience downtime due to technical issues. During these periods, your warehouse operations may come to a halt, potentially leading to missed orders, delayed deliveries, and dissatisfied customers.
Manual handling provides a level of operational resilience that can be critical in minimizing disruptions caused by maintenance and repairs. Human workers can continue to perform essential tasks even when automated machinery is out of commission.
This means that you can maintain a baseline level of productivity during maintenance intervals without the risk of a complete standstill.
Additionally, the cost and complexity of maintaining automated systems can be substantial. Skilled technicians and spare parts are necessary to keep automation equipment running smoothly, adding ongoing expenses to your budget. In contrast, training and managing a manual labor force may be more straightforward and cost-effective.
Unpredictable Workloads
Unpredictable spikes in workload are common in many industries. Whether it’s due to seasonal variations, unexpected surges in demand, or unforeseen events, your warehouse must be able to handle these fluctuations efficiently.
Manual labor provides a flexible solution for managing unpredictable workloads. When demand suddenly increases, you can quickly hire additional workers or extend the shifts of your existing workforce to meet the demand.
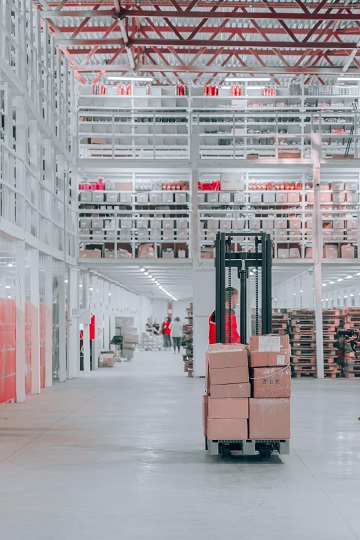
These adjustments can be made on short notice, ensuring that you can fulfill orders promptly without delays.
In contrast, relying solely on automation can lead to bottlenecks and inefficiencies during periods of high demand. Automated systems typically have fixed capacities and may not be easily scaled up to handle sudden increases in workload. This can result in missed opportunities and dissatisfied customers.
Skilled Labor Availability
The availability of skilled labor is a critical factor in the manual handling vs. warehouse automation decision. In some regions or industries, finding and retaining workers with the necessary technical skills to operate and maintain automated systems can be a significant challenge.
If your warehouse is located in an area with a shortage of qualified automation technicians or if the skill set required is highly specialized, manual labor may be a more practical option. Hiring and training manual workers may be easier and more cost-effective than recruiting and retaining skilled technicians.
Additionally, the turnover rate for manual labor can be lower than that for highly specialized automation positions, reducing the burden of constant recruitment and training. When skilled workers leave, it can be challenging to find replacements with the same level of expertise, potentially disrupting your operations.
Limited Space
Warehouses with limited physical space may find it challenging to accommodate large automated equipment. Automated systems often require dedicated areas for conveyor systems, robotic arms, and storage racks, which can be space-consuming.
Manual handling can make more efficient use of available space. Human workers can navigate tight aisles and make use of vertical space for storage more easily than automated equipment. This space efficiency can be particularly advantageous for warehouses located in urban or densely populated areas where real estate is at a premium.
By maximizing your existing space, you can reduce the need for costly facility expansions or relocations. This cost-saving benefit can make manual handling a more attractive option, especially if your warehouse operates in a confined environment.
You might also like:
- How to Organize Your Warehouse Layout: A Step-by-Step Guide for You
- Are You an Introvert or an Extrovert? Find Out Which Supply Chain Role Suits You Best!
Product Fragility
For warehouses that handle delicate or high-value products that require careful handling, manual labor can be a preferable choice. Human workers can exercise precision and judgment, adjusting their handling techniques based on the fragility and value of the items they’re dealing with.
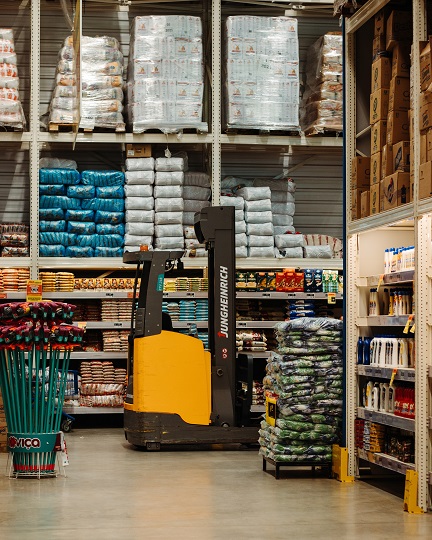
Automated systems, while efficient, may not have the same level of delicacy and adaptability when it comes to handling fragile or high-value products. This can lead to an increased risk of damage and costly losses.
Whether you’re managing fragile glassware, expensive electronics, or valuable artwork, the human touch can be more reliable in preventing accidents and ensuring that products reach customers in pristine condition.
While automation can be integrated into the process for some tasks, having skilled manual workers oversee the handling of delicate items can be a vital safeguard against damage.
Scalability
Scalability is a crucial consideration for businesses looking to grow and adapt to changing market conditions. Manual handling can be an attractive choice for small businesses or startups that want to prove their concept and gradually scale up their operations.
Manual labor offers a level of flexibility that allows you to adjust your workforce to match your growth trajectory. As your business expands and your customer base grows, you can hire additional workers or extend work hours to accommodate increased demand.
This incremental approach to scaling can help you manage your budget more effectively and ensure a smooth transition to larger-scale operations.
Furthermore, starting with manual handling allows you to refine your processes and identify areas where automation can bring the most significant benefits. You can strategically introduce automation where it makes the most sense, optimizing your operations for efficiency and cost-effectiveness.
Conclusion
The choice between manual handling and warehouse automation is not a one-size-fits-all decision. It hinges on a multitude of factors, including your business’s size, budget, product characteristics, and operational requirements.
While automation offers undeniable advantages in terms of efficiency and precision, manual handling shines in scenarios that demand flexibility, adaptability, and cost-consciousness.
By carefully assessing your specific circumstances and long-term goals, you can determine the right mix of manual labor and automation for your warehouse.
In many cases, a hybrid approach that combines the strengths of both can provide the optimal solution, allowing you to achieve efficiency while maintaining the ability to adapt to the ever-changing demands of the market.
Ultimately, the key is to make an informed decision that aligns with your unique needs and positions your business for success in the competitive world of warehousing and logistics.
I hope you find it helpful!
Please share this article with your colleagues so they can also benefit. For more insights on supply chain management, follow my LinkedIn account. You’re free to use all articles on this blog for any purpose, even for commercial use, without needing to give credit.