In the intricate world of food manufacturing, one of the most critical factors that directly impacts both product quality and profitability is shelf life management.
For those of you who work in the food manufacturing sector, you understand that maintaining the integrity of your products and raw materials is paramount. You can’t afford to let them expire.
In this blog post, we will delve deep into the intricacies of shelf life management, exploring why it is crucial and how you can establish an effective system to monitor and utilize it optimally.
Before we go further into this topic, don’t forget to follow my LinkedIn account. You’ll get more helpful insights on supply chain management there.
Table of Contents
Why is Shelf Life Management Important?
Shelf life management is the process of ensuring that both your products and raw materials are used or sold before they expire.
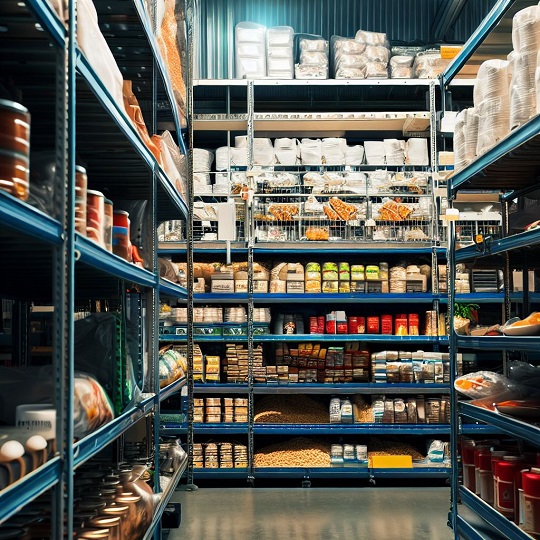
The significance of this practice cannot be overstated, as it affects various aspects of your business, including quality control, compliance, and profitability.
Let’s take a closer look at why shelf life management is essential:
- Quality Assurance: The quality and safety of your products are directly linked to their shelf life. As time passes, the nutritional value, taste, texture, and safety of your food products can deteriorate. Proper shelf life management ensures that consumers receive products at their peak quality.
- Compliance: Regulatory bodies impose strict guidelines on food manufacturing, including labeling requirements that specify the use-by or best-before dates. Failure to comply with these regulations can result in fines, recalls, and damage to your brand’s reputation.
- Reduced Waste: Efficient shelf life management minimizes the risk of products expiring and being discarded. This translates to less waste and cost savings for your company.
- Customer Satisfaction: Consistently delivering fresh and high-quality products enhances customer satisfaction and fosters brand loyalty.
Now that we understand the importance of shelf life management, let’s explore how to establish an effective system to monitor and utilize it effectively.
Establishing an Effective Shelf Life Management System
- Know Your Products:
- Start by comprehensively understanding the characteristics of each product in your inventory.
- Identify the critical factors that affect shelf life, such as ingredients, packaging, storage conditions, and processing methods.
- Categorize products based on their shelf life, grouping them into short shelf life, medium shelf life, and long shelf life categories.
- Implement Proper Storage Conditions:
- Ensure that your storage facilities are designed to maintain the optimal environment for different product categories. This includes temperature, humidity, and light control.
- Implement a first-in, first-out (FIFO) inventory system to prevent older products from sitting on the shelves for extended periods.
- Labeling and Documentation:
- Clearly label each product with its production date, use-by date, and batch/lot numbers.
- Maintain meticulous records of incoming raw materials and outgoing finished products, including dates and quantities.
- Invest in inventory management software to streamline the tracking and monitoring process.
- Regular Quality Testing:
- Establish a routine testing schedule to evaluate the quality and safety of products nearing their expiration date.
- Conduct sensory evaluations, microbiological tests, and chemical analyses to ensure products meet quality standards.
- Supplier Relationships:
- Maintain open communication with your suppliers to stay informed about changes in raw materials and their shelf life.
- Collaborate with suppliers to optimize packaging and storage recommendations for extended shelf life.
- Employee Training:
- Educate your staff on the importance of shelf life management and proper handling procedures.
- Provide training on identifying signs of product spoilage and the appropriate actions to take.
- Inventory Rotation:
- Develop a systematic approach to rotate inventory to minimize the risk of products nearing expiration.
- Product Redistribution:
- If you foresee surplus inventory nearing its expiration date, explore options for redistributing it within your distribution network or donating it to charitable organizations.
- Consumer Education:
- Educate consumers about the significance of use-by and best-before dates through clear and informative packaging.
- Encourage responsible consumption and proper storage practices.
- Continuous Improvement:
- Regularly review and update your shelf life management procedures based on industry best practices, feedback, and evolving regulations.
You might also like:
- Exploring Supply Chain Costs: Everything You Need to Know
- The Vital Role of Production Planning and Inventory Control (PPIC): Ensuring Efficiency and Success
- How to Dodge Negotiation Pitfalls: 10 Mistakes You Can Avoid for Success
Conclusion
For those working in the food manufacturing sector, effective shelf life management is not just a good practice; it’s a fundamental necessity.
It ensures that your products meet quality standards, comply with regulations, and reduce waste, ultimately contributing to the success and sustainability of your business.
By understanding the unique characteristics of your products, implementing proper storage conditions, maintaining accurate documentation, and fostering strong supplier relationships, you can master the art of shelf life management.
Continuous improvement and a commitment to delivering the freshest and safest products to consumers will set your brand apart and drive long-term success in the competitive world of food manufacturing.
I hope you find it helpful!
Please share this article with your colleagues so they can also benefit. For more insights on supply chain management, follow my LinkedIn account. You’re free to use all articles on this blog for any purpose, even for commercial use, without needing to give credit.