In the intricate world of manufacturing, one of the most fundamental and strategic decisions a company must make is whether to produce its components, products, or services in-house (make) or to source them from external suppliers (buy).
This decision can have far-reaching consequences for a company’s profitability, competitiveness, and long-term viability.
In this comprehensive blog post, we will delve into the myriad factors that influence the make-or-buy decision in manufacturing.
By the end of this exploration, you will have a clearer understanding of the complex interplay of elements that guide this critical choice.
Before we go further into this topic, don’t forget to follow my LinkedIn account. You’ll get more helpful insights on supply chain management there.
Table of Contents
Cost Analysis: The Foundation of the Decision
The first and foremost factor that companies consider when making the make-or-buy decision is cost analysis. It’s about weighing the financial implications of producing an item in-house against purchasing it from external suppliers.
Here’s a closer look at the financial aspects that play a pivotal role.
Production Costs
Production costs include everything required to manufacture a product within your organization. These costs encompass raw materials, labor, overhead, equipment, maintenance, utilities, and more. Understanding these costs in detail is essential to make an informed decision.
The primary advantage of producing in-house is cost control. You have a clear view of all the expenses involved, and you can implement cost-cutting measures more effectively.
Purchasing Costs
On the other hand, purchasing costs are associated with acquiring products or components from external suppliers.
This includes the purchase price, shipping fees, and any other charges directly linked to acquiring the product.
It’s crucial to examine supplier contracts to understand the total cost of acquisition fully.
Economies of Scale
Economies of scale refer to the cost advantages that result from increased production.
In-house production can benefit from these economies, potentially reducing the per-unit production cost as production volumes increase.
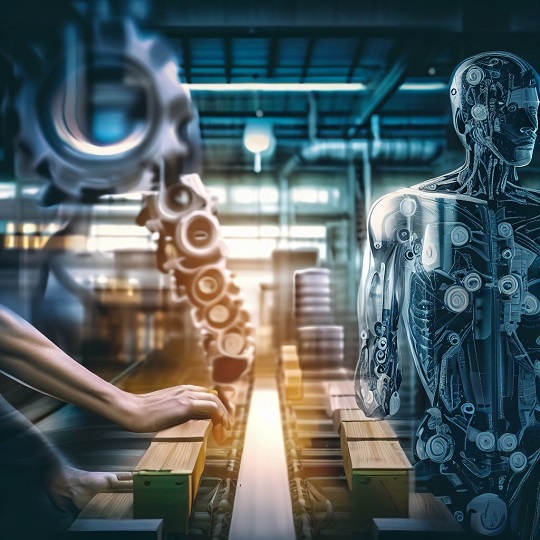
It’s vital to analyze whether your production volume justifies these cost advantages.
Capacity and Capability: Do You Have What It Takes?
Capacity and capability are fundamental to the make-or-buy decision. This entails assessing whether your company possesses the necessary resources, expertise, and infrastructure to manufacture the product effectively.
In-House Expertise
Having the right expertise within your organization is essential.
Skilled labor, engineering talent, and process knowledge are all critical to ensure the product is produced to the required standards.
When you make in-house, you have direct control over the knowledge and skills of your team.
Production Capacity
Evaluate your production facilities and their current and potential capacity.
Can your existing infrastructure meet the present and future demand for the product?
Assess whether expanding or upgrading your facilities is a viable and cost-effective option.
You might also like:
Quality and Control: A Balancing Act
The quality of the product and the level of control you can exert over the manufacturing process are crucial considerations in the make-or-buy decision.
Quality Standards
Meeting quality standards is non-negotiable, regardless of your decision.
However, you must weigh whether in-house production can consistently meet the necessary quality standards or if external suppliers have a better track record in this regard.
Quality Control
Control over the manufacturing process is a significant advantage of in-house production. It allows for real-time monitoring, adjustments, and immediate response to quality issues.
When you buy from external suppliers, this control may be limited.
Lead Time and Flexibility: Time Matters
The lead time required to produce or acquire a product can significantly impact your ability to respond to market demands and changes. Additionally, flexibility in your manufacturing process is a crucial asset.
Lead Time
Consider the lead times for in-house production versus those for external suppliers.
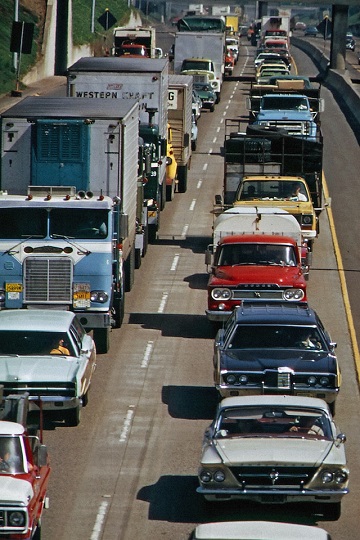
In-house production can be faster and more responsive, which is especially beneficial when dealing with sudden changes in demand.
Flexibility
Manufacturing processes that are controlled in-house are generally more adaptable to changes in product specifications or design. This is a significant advantage when your products require frequent updates or customization.
Risk Management: Mitigating Potential Pitfalls
Risk management is an integral part of any strategic decision-making process. This includes assessing risks related to the supply chain, capital investment, and more.
Supply Chain Risk
External suppliers can introduce supply chain risks, such as disruptions, quality issues, or price fluctuations. It’s essential to assess these risks and have mitigation strategies in place.
Capital Investment Risk
Investing in manufacturing facilities and equipment carries its own set of risks. These include the potential for overcapacity or the need for expensive upgrades as technology evolves. A thorough risk assessment is crucial.
Strategic Considerations: Aligning with Your Goals
Your make-or-buy decision should align with your company’s strategic goals. This involves considering your core competencies, the potential for vertical integration, and your long-term vision.
Core Competencies
Consider whether manufacturing is a core competency of your company. If not, it might be more strategic to focus on other areas of your business and outsource non-core components.
Vertical Integration
Vertical integration refers to owning more of the supply chain, from raw materials to distribution. It can provide greater control and flexibility, but it also demands substantial resources and commitment.
Regulatory and Compliance: Staying on the Right Side of the Law
Ensuring that the products you manufacture or acquire comply with industry regulations and standards is crucial for avoiding legal and financial consequences.
Intellectual Property: Guarding Your Secrets
The protection of intellectual property is a critical factor to consider.
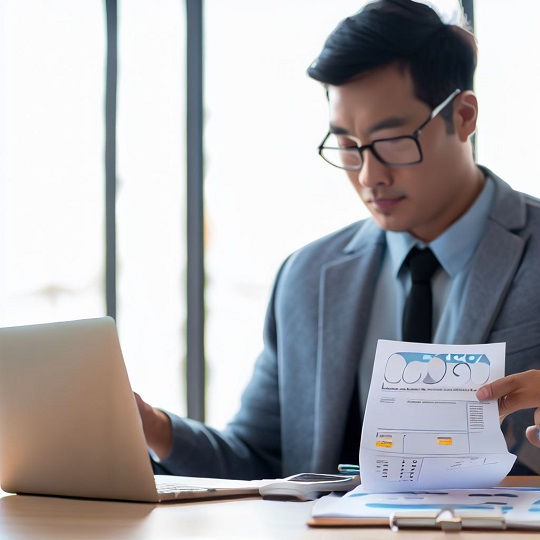
In-house production can provide better control over proprietary processes and technologies, minimizing the risk of IP leaks.
Supplier Relationships: Building Trust
The relationships you establish with your suppliers can have a significant impact on your production process. Reliability, performance, and long-term partnership potential should all be assessed.
You might also like:
- 33 Strategies How to Significantly Reducing Supply Chain Lead Times
- How Challenging Should Supply Chain KPI Targets be Set?
Cost of Transition: The Bridge Between Decisions
Transitioning from one production method to another is not without its costs. This includes retooling, retraining, and managing any contractual commitments with suppliers or changes to your in-house operations.
Market Conditions: Adapting to the World Outside
External factors, such as competitive pressures, customer expectations, and market pricing, can influence your make-or-buy decision. Staying in tune with the market is vital.
Environmental and Sustainability Factors: Going Green
The global focus on environmental sustainability adds another layer of complexity to the decision-making process. Consider the environmental impact of both in-house production and outsourcing, as well as alignment with sustainability goals and regulations.
Geopolitical Considerations: The Bigger Picture
Geopolitical factors can affect the availability and cost of materials or the stability of supply chains. These factors can disrupt production or sourcing strategies, so it’s important to monitor and adapt to changing geopolitical landscapes.
Conclusion
The make-or-buy decision in manufacturing is a multifaceted process that involves careful consideration of numerous factors.
By understanding and analyzing these factors thoroughly, you can make a decision that aligns with your company’s goals and enhances your competitiveness in the ever-evolving landscape of the manufacturing industry.
Remember that this decision is not static; it may evolve over time as your company’s capabilities and market conditions change.
Ultimately, a well-informed make-or-buy decision can be a strategic asset for your organization, contributing to its long-term success and profitability.
I hope you find it helpful!
Please share this article with your colleagues so they can also benefit. For more insights on supply chain management, follow my LinkedIn account. You’re free to use all articles on this blog for any purpose, even for commercial use, without needing to give credit.