Efficiency is the cornerstone of a successful supply chain. In today’s fast-paced business landscape, customers expect quick and reliable delivery of products.
To meet these demands and gain a competitive edge, reducing supply chain lead times has become a paramount goal for businesses of all sizes and industries. Shorter lead times can help streamline operations, cut costs, and improve customer satisfaction.
In this comprehensive blog post, we’ll delve into a multitude of strategies and best practices for significantly reducing supply chain lead times.
From demand forecasting and inventory management to technology integration and risk management, we’ll explore how each element contributes to the overall goal of achieving faster and more efficient supply chains.
Let’s get started on the journey to optimizing your supply chain and gaining a competitive advantage through lead time reduction.
Before we go further into this topic, don’t forget to follow my LinkedIn account. You’ll get more helpful insights on supply chain management there.
Table of Contents
Demand Forecasting
Demand forecasting is the foundation upon which supply chain lead time reduction strategies are built.
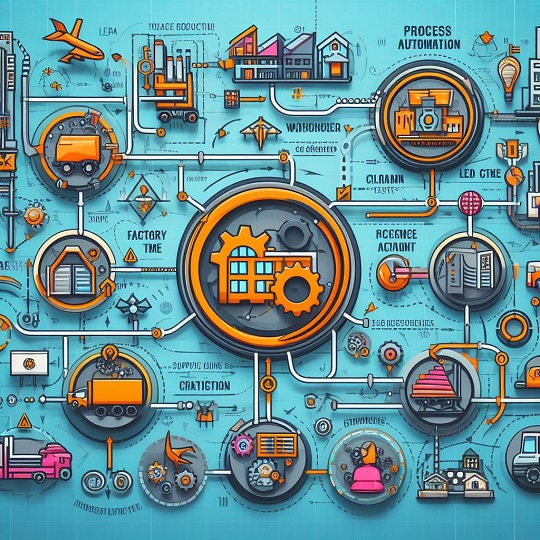
Accurate forecasts enable businesses to understand customer needs better, anticipate demand fluctuations, and plan production and inventory accordingly. Here’s how you can improve demand forecasting:
- Historical Data Analysis: Analyze historical sales data, market trends, and seasonal patterns to identify demand patterns.
- Advanced Analytics: Utilize advanced analytics tools and machine learning algorithms to improve the accuracy of demand forecasts.
- Collaboration: Foster collaboration between sales, marketing, and supply chain teams to gain insights into upcoming promotions or product launches that might affect demand.
Inventory Management
Effective inventory management is crucial for reducing lead times while maintaining customer service levels. Two key approaches to consider are just-in-time (JIT) and lean inventory practices:
- Just-in-Time (JIT): JIT inventory management aims to minimize excess inventory by receiving and producing goods just in time to meet customer demand. This approach helps lower lead times by reducing the need for storage space and the risk of holding obsolete inventory.
- Lean Inventory Practices: Implement lean principles to optimize inventory levels while maintaining quality and service levels. This involves reducing safety stock levels and continually evaluating your inventory to eliminate waste.
Supplier Relationships
Strong relationships with key suppliers are essential for achieving shorter lead times. Collaborating closely with suppliers can streamline processes and ensure a reliable supply of materials. Here’s how to nurture these relationships:
- Open Communication: Maintain open and transparent communication channels with suppliers to share information on demand forecasts, production plans, and potential issues.
- Supplier Scorecards: Develop supplier scorecards to assess and monitor supplier performance regularly. Encourage suppliers to meet or exceed agreed-upon lead times and quality standards.
Supplier Diversification
Relying on a single supplier for critical components or materials can pose significant risks to your supply chain. To mitigate these risks and reduce lead time vulnerabilities, consider supplier diversification:
- Multiple Suppliers: Work with multiple suppliers for essential components or materials. This approach provides backup options if one supplier encounters issues.
- Risk Assessment: Assess the geographic and operational risks associated with each supplier and develop contingency plans to address potential disruptions.
Production Efficiency
Optimizing production processes is a fundamental step in reducing lead times. By reducing cycle times and increasing throughput, you can significantly cut the time it takes to bring products to market:
- Lean Manufacturing: Implement lean manufacturing principles to identify and eliminate inefficiencies in your production processes.
- Automation: Invest in automation technologies to streamline production and reduce manual labor, which can slow down processes.
- Layout Optimization: Reorganize your manufacturing layout to minimize bottlenecks and improve the flow of materials and products.
You might also like:
Transportation Optimization
Efficient transportation and logistics operations are critical for delivering products to customers on time. Optimization strategies can help reduce transportation lead times:
- Dedicated Transportation Services: Consider dedicated transportation services to ensure timely and reliable deliveries.
- Route Optimization: Implement route optimization software to find the most efficient routes for your shipments, reducing transit times and costs.
- Express Shipping: When necessary, use express shipping options to expedite deliveries to customers and reduce lead times.
Lead Time Reduction Projects
Initiating specific projects focused on reducing lead times within your supply chain can yield significant improvements. Consider these targeted efforts:
- Order Processing Time: Streamline order processing by automating manual tasks and reducing paperwork.
- Manufacturing Lead Times: Implement strategies such as setup time reduction and batch size optimization to shorten manufacturing lead times.
- Transportation Lead Times: Collaborate with carriers and logistics providers to identify opportunities for reducing transportation lead times.
Technology Integration
Leveraging advanced technologies can enhance visibility and traceability across the supply chain, allowing you to respond quickly to disruptions and reduce lead times:
- RFID (Radio-Frequency Identification): Implement RFID technology for real-time tracking of products and materials within your supply chain.
- IoT (Internet of Things): Use IoT sensors to monitor equipment, shipments, and inventory in real time, enabling proactive issue resolution.
- Blockchain: Explore blockchain solutions for secure and transparent supply chain transactions, which can enhance trust and traceability.
Cross-Functional Collaboration
Effective collaboration between different departments within your organization is crucial for identifying and addressing lead time bottlenecks:
- Procurement, Production, and Logistics Collaboration: Promote open communication and collaboration between these departments to ensure seamless coordination.
- Data Sharing: Share relevant data and insights across teams to facilitate decision-making and problem-solving.
Continuous Improvement
Embracing a culture of continuous improvement is essential for sustained lead time reduction:
- Lean and Six Sigma Principles: Apply Lean and Six Sigma methodologies to identify and eliminate inefficiencies systematically.
- Kaizen Events: Conduct Kaizen events to gather employees’ input and make incremental improvements to processes.
Data Analytics
Harness the power of data analytics to identify trends and potential issues within your supply chain:
- Data Collection: Collect and analyze data from various sources, including production, transportation, and inventory systems.
- Predictive Modeling: Use predictive modeling to forecast demand, detect anomalies, and optimize supply chain processes.
You might also like:
- More Than Just Tech Problems: How Supply Chain Managers Handle People and Processes in Many Ways
- The Complete Guide to Creating Useful Item Codes for Efficient Material Management in ERP Systems
Risk Management
Developing a robust risk management strategy is crucial for mitigating the impact of unforeseen events on your supply chain:
- Risk Assessment: Identify potential risks, such as natural disasters or geopolitical disruptions, and assess their potential impact on your supply chain.
- Contingency Planning: Develop contingency plans that outline steps to take in the event of supply chain disruptions, with a focus on minimizing lead time impacts.
Customer Collaboration
Collaborating closely with your customers is key to aligning your supply chain processes with their needs and expectations:
- Customer Insights: Gather customer feedback and insights to better understand their requirements and preferences.
- Demand Alignment: Work with customers to align demand forecasts and order patterns, reducing the risk of supply-demand mismatches.
Lead Time Monitoring
Continuous monitoring and measurement of lead times at various supply chain stages are essential for tracking progress and identifying areas for improvement:
- Key Performance Indicators (KPIs): Establish KPIs related to lead times and regularly review performance against these metrics.
- Real-Time Tracking: Implement real-time tracking systems to monitor the status of orders and shipments.
Conclusion
Reducing supply chain lead times is an ongoing process that requires commitment, collaboration, and a holistic approach.
By implementing these 33 strategies and continuously seeking ways to optimize your supply chain, you can achieve shorter lead times, which, in turn, can lead to cost savings, improved customer satisfaction, and a competitive advantage in today’s dynamic business environment.
Remember, there is no one-size-fits-all solution, and the effectiveness of these strategies may vary depending on your industry and specific supply chain challenges.
To succeed, adapt and tailor these approaches to meet your unique needs and continually refine your supply chain processes for maximum efficiency and responsiveness.
I hope you find it helpful!
Please share this article with your colleagues so they can also benefit. For more insights on supply chain management, follow my LinkedIn account. You’re free to use all articles on this blog for any purpose, even for commercial use, without needing to give credit.