In today’s dynamic business landscape, successful supply chain planning is essential for maintaining your operational efficiency, meeting your customer demands, and maximizing your profitability.
However, when you’re dealing with suppliers whose lead times vary, the complexity of managing your supply chain increases significantly.
In this blog post, we will delve into the intricacies of creating an effective supply chain plan in the face of these variable supplier lead times.
We’ll explore strategies and best practices that will help you ensure smooth operations and customer satisfaction.
But, before we delve deeper into this topic, make sure you have also followed my LinkedIn account to gain more insights on supply chain management.
Table of Contents
Understanding Variable Supplier Lead Times
Let’s break down what we mean by variable supplier lead times.
When you place an order for products or materials, supplier lead time refers to the time it takes for that order to be fulfilled – from the moment you make the request to when the products or materials are delivered to you.
However, what makes it “variable” is that different suppliers might take different amounts of time to complete this process.
So, why does this variability happen?
Well, it’s due to a range of factors that can influence how long it takes for your order to reach you.
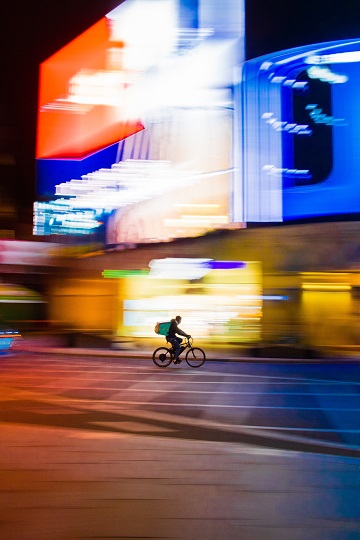
These factors include things like where the supplier is located geographically, how much production capacity they have at the moment, any constraints related to transportation, and how reliable the supplier’s operations are. All these elements contribute to the variations in lead times among different suppliers.
In simpler terms, variable supplier lead times mean that the time it takes for your orders to be fulfilled can differ depending on which supplier you’re dealing with. This can have a significant impact on your supply chain planning and how smoothly your operations run.
Challenges Posed by Variable Lead Times
Now that we’ve discussed what variable supplier lead times are, let’s dive into the challenges that you can face when dealing with these fluctuations in your supply chain planning process:
Forecast Accuracy
When lead times from suppliers vary, accurate forecasting becomes even more crucial for you. Why? Because if you make a small error in your forecasts, it could have significant consequences.
For instance, if you underestimate demand and your suppliers take longer than expected, you might end up with stockouts – meaning you don’t have enough products to meet customer orders.
On the other hand, overestimating demand and having longer lead times can result in overstocking, tying up your resources unnecessarily and driving up operational costs.
You might also like:
- Are You an Introvert or an Extrovert? Find Out Which Supply Chain Role Suits You Best!
- Are You Maximizing Efficiency in Managing Products with Short Shelf Life?
Inventory Management
The challenge of balancing your inventory levels becomes more complex when you’re dealing with suppliers whose lead times differ.
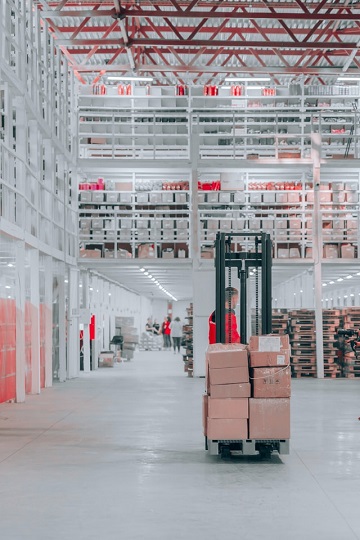
Imagine you have some suppliers who deliver quickly and others who take longer. You need to find the right balance of inventory to cover you during those varying lead times. If you stock too much, you tie up your working capital in excess inventory.
On the flip side, if you stock too little and lead times are longer than expected, you’ll miss out on potential sales opportunities and risk disappointing your customers.
Demand Fluctuations
Think about the impact of sudden changes in demand when you have suppliers with different lead times. If there’s a spike in demand, suppliers with shorter lead times might be able to react quickly, but those with longer lead times could struggle to keep up. This creates a ripple effect that can lead to stockouts or excess inventory.
In other words, the variability in lead times can amplify the risks associated with demand fluctuations.
Operational Efficiency
The variability in lead times among your suppliers can disrupt your production schedules and how you allocate your resources.
Let’s say you have a tight production schedule that relies on timely deliveries from various suppliers. If even one supplier experiences delays, it can cause a domino effect, impacting your overall operational efficiency.
Plus, you might need to allocate resources differently to accommodate these fluctuations, which can be challenging and inefficient.
In essence, dealing with suppliers with varying lead times can introduce complexities that affect your forecasting, inventory management, responsiveness to demand changes, and the overall efficiency of your operations.
Being able to navigate and mitigate these challenges is key to maintaining a well-functioning supply chain and delivering a satisfying experience to your customers.
Strategies for Effective Supply Chain Planning with Variable Lead Times
Now that we’ve covered the challenges you might encounter due to varying supplier lead times, let’s explore some strategies that you can adopt to overcome these challenges and ensure your supply chain planning remains effective.
Diversify Your Suppliers
To manage the risks associated with lead time variability, consider diversifying your supplier base. This means engaging with multiple suppliers for critical components or products. By having alternatives in place, you’ll be better equipped to handle fluctuations in lead times from different sources.
Optimize Safety Stock
Maintaining safety stock levels can act as a safety net against demand fluctuations and longer lead times. Use statistical models and historical data to calculate the optimal amount of safety stock for each specific item in your inventory.
You might also like:
- Adapt and Thrive: Why You Need Creative Thinking in Supply Chain Management
- Drive Profitability with Precise Demand Forecasting – Here’s How You Can Do It
Implement Dynamic Forecasting
A dynamic forecasting approach can help you adapt to changing circumstances. By considering current demand trends and using real-time data, you can adjust your forecasts accordingly. Collaborate closely with your sales and marketing teams to gain valuable insights that can further refine your forecasts.
Buffer Your Lead Times
When you’re placing orders with suppliers, consider introducing a buffer into your lead time estimates. This extra time can help you manage any unexpected delays more effectively and provide a cushion for potential disruptions in your supply chain.
Build Collaborative Relationships
Establishing open and collaborative relationships with your suppliers is essential. Transparency and effective communication can help you gain a better understanding of potential lead time variations, enabling you to anticipate and plan for them more effectively.
Leverage Technology Integration
Advanced supply chain management software can be a valuable asset in this context. Look for software that can factor in variable lead times when generating production schedules, inventory plans, and order quantities. This technological support can enhance your planning accuracy.
Adopt Demand-Driven Planning
Shifting from traditional push-based planning to demand-driven planning can be beneficial. This approach centers on responding to the actual demand rather than just pushing out products. By doing so, you can minimize the impact of lead time variability.
Utilize Data Analytics
Take advantage of data analytics to monitor your supplier performance and track lead time trends. By identifying patterns and outliers, you can make well-informed decisions that optimize your lead time management.
Plan for Different Scenarios
It’s always wise to be prepared for various lead time scenarios. Developing contingency plans allows you to react swiftly and effectively when unexpected situations arise. This proactive approach can help you minimize disruptions to your operations.
Strive for Continuous Improvement
Regularly assess and refine your supply chain processes. Involve your stakeholders and gather feedback to identify areas for improvement. Monitor key performance indicators to ensure you’re making progress and maintaining a high level of efficiency.
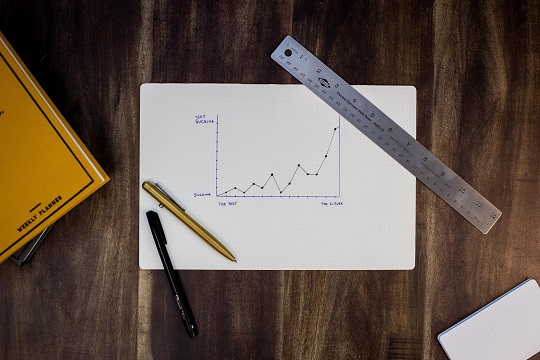
Incorporating these strategies into your supply chain planning can empower you to navigate the challenges posed by variable lead times. Remember, the key lies in adaptability, collaboration, and utilizing technology to your advantage. By doing so, you can optimize your operations, enhance customer satisfaction, and set your business on a path of sustained success in a dynamic marketplace.
Conclusion
In conclusion, mastering your supply chain planning in the face of variable supplier lead times demands a strategic and proactive stance from you.
By diversifying your suppliers, fine-tuning your safety stock levels, harnessing the potential of technology, and nurturing collaborative relationships, you can adeptly steer through the intricacies of lead time variability.
These actions will not only uphold your operational efficiency but also ensure the satisfaction of your customers.
In an ever-evolving global marketplace, your ability to excel in supply chain planning despite variable lead times will stand out as a crucial factor that sets you apart and propels your success forward.
Top of Form
Bottom of Form
Hope it is useful!
Please share this article with your colleagues as well, so that they can also benefit from it. Follow my LinkedIn account for more insights on supply chain management. All articles on this blog are free for you to use for any purpose, including commercial use, without the need for attribution.