Table of Contents
The Holiday Rush Is Here – Are You Ready?
Picture this. The year is winding down, the holiday season is in full swing, and people are either traveling to see their families or frantically shopping for last-minute gifts. Roads are packed, warehouses are overflowing, and everyone in the supply chain industry is holding their breath. It’s peak season—the time of year when demand skyrockets, lead times stretch, and shipping constraints make everything feel like an uphill battle.
If you’ve been in supply chain long enough, you know how this story goes. One delayed shipment leads to a stockout. Customers grow impatient, flooding your support team with complaints. Meanwhile, transportation is a nightmare. Government-imposed road restrictions on large trucks mean deliveries are either delayed or rerouted, causing further disruptions.
The pressure is relentless, but that doesn’t mean your business has to suffer. The key is preparation, adaptability, and having the right strategies in place before the chaos begins.
Before we go further into this topic, don’t forget to follow my LinkedIn account. You’ll get more helpful insights on supply chain management there.
The Lead Time Puzzle – Why Everything Takes Longer
One of the biggest headaches during the holiday season is extended lead times. Suppliers are overwhelmed, manufacturers are working overtime, and every carrier is operating at full capacity. If a shipment that usually takes three days to arrive suddenly stretches to seven or ten, the ripple effect can be devastating.
This is where proactive planning makes all the difference. Businesses that anticipate delays and adjust their inventory levels accordingly have a significant advantage. Instead of operating with just-in-time inventory, shifting to a just-in-case mindset can help cushion the impact of late shipments. Stocking up on high-demand items ahead of time might feel like an extra cost, but it’s often the difference between fulfilling orders smoothly and losing sales due to stockouts.
You might also like:
- Why Your Supply Chain Will Never Be Perfect and That’s Okay
- Do You Really Need a 3PL or Can You Handle Logistics In-House?
Road Restrictions and Delivery Nightmares
Now, let’s talk about another major holiday season roadblock—literally. Many countries impose travel restrictions on large trucks during peak holiday periods to ease traffic congestion and accommodate holiday travelers. This means limited delivery windows, rerouted shipments, and longer transit times.
The worst thing you can do is wait until the restrictions take effect before making adjustments. If your business relies on heavy trucks for transportation, working closely with your logistics partners is critical. Rescheduling deliveries for off-peak hours, securing alternative routes, or even using smaller vehicles for last-mile deliveries can help minimize disruptions. Some companies even build micro-fulfillment centers in key locations to shorten delivery distances and reduce dependency on long-haul trucking.
Keeping Customers Happy When Delays Are Inevitable
No matter how well you prepare, delays are sometimes unavoidable. When that happens, transparency is your best tool for keeping customers satisfied. People may not like waiting longer for their orders, but they appreciate honesty. The worst thing you can do is leave them in the dark.
Updating estimated delivery times on your website, sending real-time tracking updates, and providing proactive communication about delays can help manage expectations. Some companies go a step further by offering small discounts, free shipping on future orders, or loyalty points to compensate for delays. These gestures may seem minor, but they can make a huge difference in maintaining customer trust.
Warehouse Overload and Order Fulfillment Pressure
With sales peaking, warehouses become war zones. Workers are scrambling to pick, pack, and ship thousands of orders while dealing with inventory shortages, misplaced stock, and an overwhelming number of returns. If your fulfillment process isn’t optimized, you’re setting yourself up for disaster.
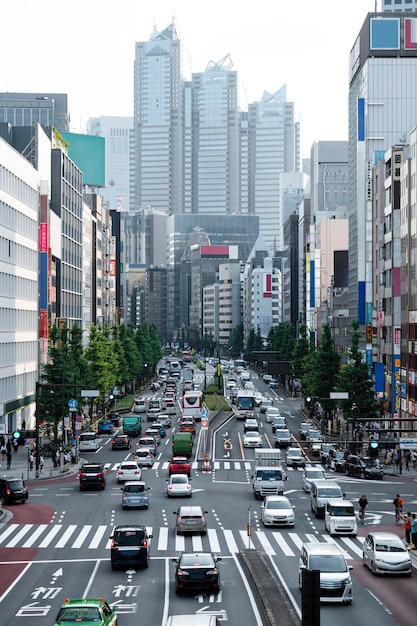
Automation can be a game-changer. Investing in warehouse management systems (WMS), barcode scanning, and real-time inventory tracking can significantly reduce errors and improve efficiency. Another strategy is implementing zone picking, where workers are assigned to specific sections of the warehouse instead of running all over the place. This speeds up order fulfillment and reduces bottlenecks.
Cross-training employees is another smart move. When demand surges, having flexible workers who can switch between roles—such as picking, packing, and quality control—ensures smoother operations. The last thing you want is a backlog of unprocessed orders because your team can’t keep up.
You might also like:
- Feeling Overwhelmed by Supply Chain Chaos? Here’s How an Action Plan with Milestones Can Save You
- How Complex Is Supply Chain Management Really and Why Does It Seem So Overwhelming?
The Role of Data in Surviving Peak Season
If you’re relying on guesswork to manage your holiday supply chain, you’re already at a disadvantage. Data is your best ally. Analyzing historical sales trends, demand forecasting, and tracking supplier performance can help you make informed decisions.
Advanced analytics and AI-driven forecasting tools allow businesses to predict demand spikes and adjust procurement strategies accordingly. Instead of reacting to problems as they arise, you can proactively identify which products need to be stocked in higher volumes, which suppliers are most reliable, and where potential bottlenecks may occur.
Real-time visibility is equally important. If you’re constantly asking, “Where’s my shipment?” instead of checking a live dashboard, it’s time to upgrade your tracking systems. Having real-time insights into your supply chain allows you to address issues before they escalate.
Contingency Planning – Because Things Will Go Wrong
Even with the best preparation, disruptions will happen. That’s why having a contingency plan is crucial. What will you do if your main supplier fails to deliver? What’s the backup plan if road restrictions prevent on-time shipments? How will you handle a warehouse breakdown at peak demand?
Having alternative suppliers on standby, securing multiple carriers, and diversifying fulfillment centers can help mitigate risks. Many businesses also create emergency response teams that can quickly troubleshoot supply chain disruptions and implement backup strategies. The more agile your business, the better you’ll navigate holiday season chaos.
Final Thoughts – Staying Ahead in the Holiday Madness
Peak season doesn’t have to be a logistical nightmare. With the right planning, supply chain resilience, and proactive decision-making, businesses can turn holiday challenges into opportunities. From stocking up in advance and optimizing warehouse operations to leveraging data and communicating transparently with customers, every step you take now will determine how smoothly things run when the holiday rush is in full swing.
The companies that thrive during this period aren’t necessarily the biggest ones with unlimited resources—they’re the ones that anticipate challenges, adapt quickly, and put customer experience first. So, as the holiday season approaches, ask yourself: is your supply chain ready for what’s coming?
I hope you find it helpful!
Please share this article with your colleagues so they can also benefit. For more insights on supply chain management, follow my LinkedIn account. You’re free to use all articles on this blog for any purpose, even for commercial use, without needing to give credit.